Software – Interoperability in construction
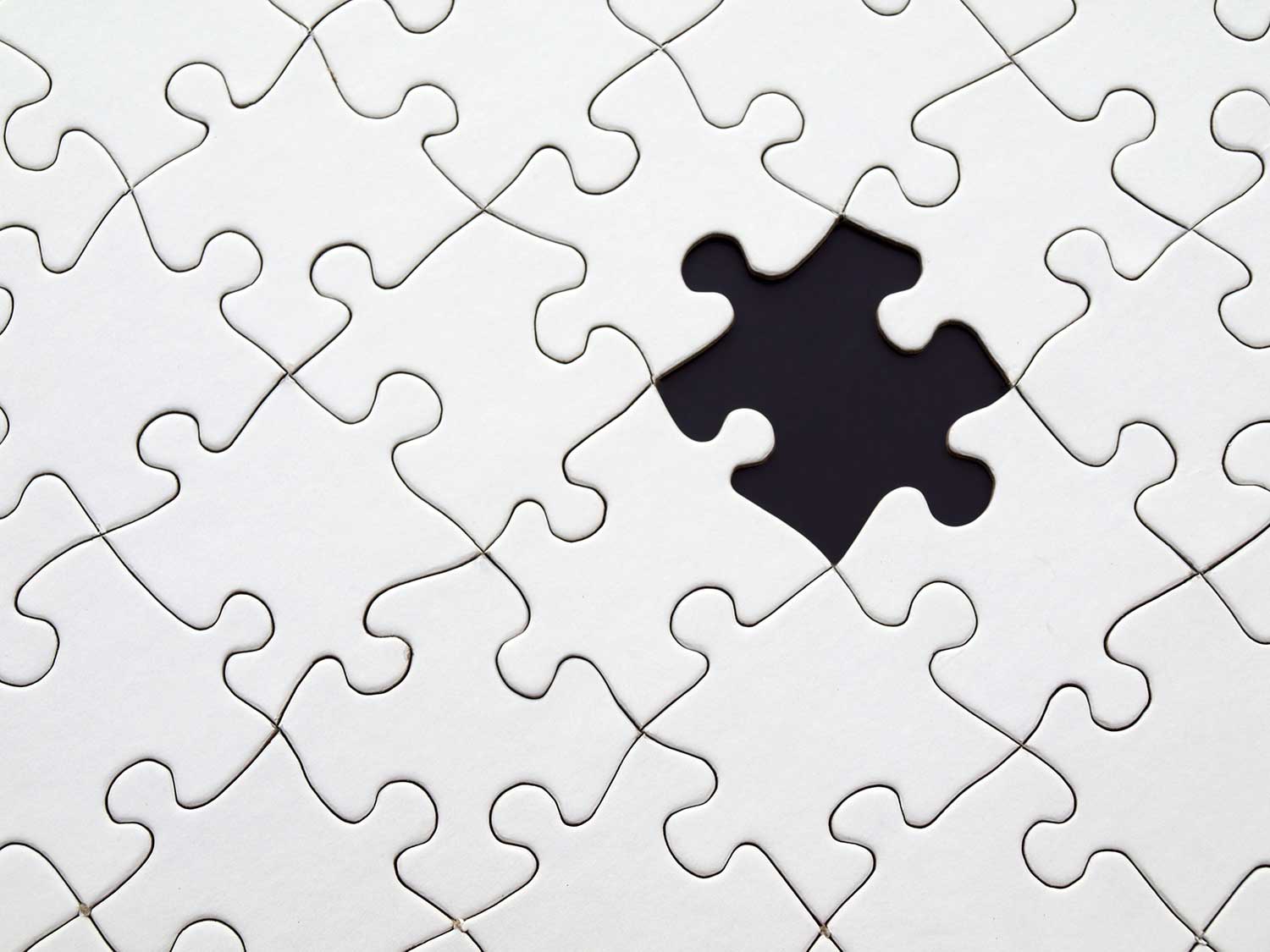
Interoperability in construction: Understanding (and beating) the silent killer
What is interoperability?
Outside of IT, software engineering and a few other technical sectors, interoperability isn't a commonly used term. But it is a term which perfectly encapsulates one of the major issues which has been plaguing (and continues to plague) the construction and other industrial companies.
So let's 'define' interoperability, and then explain what it means in practical terms.
Interoperability is a characteristic of a product or system which enables it to work or communicate directly with other products or systems - or be 'compatible' with other systems.
Interoperability is a systems ability to operate with another external system, hence 'inter' meaning mutually, reciprocally, together, during and 'operability' meaning to the ability to keep equipment, a system or a whole industrial installation in a safe and reliable functioning condition.
In simple terms, interoperability allows systems and the people behind those systems to easily exchange and use information.
Why does interoperability matter in the construction industry?
So you're probably still wondering why this interoperability matters to companies who are building bridges and digging tunnels.
It matters because a lack of interoperability is costing construction and industrial companies millions and millions of productive hours and resulting in projects being delivered late and over budget.
And how is it doing this?
Every day, millions of people in the construction industry use fragmented systems, softwares, standalone apps and paper to capture and communicate what's happening on site, in the office, with suppliers, with deliveries, with variations and every other moving part necessary to deliver any project.
Most of these systems and tools don't communicate with one another; they aren't interoperable:
- The information written down on a piece of paper can't be easily exchanged or used by a computer
- The information captured in a standalone site diary app can't be easily exchanged or used by your standalone safety checklist software
- The information captured on word docs can't be easily exchanged with a spreadsheet
So what does this mean for the daily operations of your company?
It means you need human beings - including administrators, foremen, engineers and project managers to spend their time transferring data between systems.
It means every day, highly trained engineers spending hours reconciling timesheet, production, financial and other information into spreadsheets, financial systems and other tools.
These people serve as the connector between systems - because the systems can't communicate with each other. A word doc can't send it's data or information straight into the spreadsheet because it doesn't understand how to format that information in a way which 'matches' the word document.
So a person must sit down, read through the word doc, create and format a spreadsheet, and then spend their time manually entering that same information. This type of double-handling would never fly on site.
The only other solution available to companies is integrations and other tools like mail merge. And while software integrations continue to get better and better, they still often require bespoke work which costs tens of thousands if not millions of dollars (if you want proof of the interoperability problem, just look at the market for integration vendors, providers and consultants).
So why isn't everything interoperable?
Because systems and softwares were designed to do single or relatively narrow job:
- Microsoft word is a word processor
- Microsoft excel and other spreadsheet softwares are designed to arrange data in the rows and columns of a grid, to be manipulated and used in calculations
- PDF is a file format for capturing and sending electronic documents in exactly the intended format
Looking at the definition of a PDF, it's designed to capture and send a document in the exact intended format. That's great for ensuring that the document looks great and has your logo in the top corner, but what about when you want to use the data from a PDF, or transfer the data from that PDF into another system.
Once again, a human must convert that 'exact' format into another source of information so that it can be used. On a PDF, the information is only useful to humans who can read it or computers who can scan it as an image.
Word documents, spreadsheets, accounting systems like Xero and PDFs weren't designed to pass data and information from site to the office and back again.
In other words, these systems weren't designed or built for the construction industry (nor oil and gas, mining, forestry etc.)
They are systems and tools which the construction industry amongst others have adopted because they 'work'. And they are amazing at what they do. They have become so well known and so easy to use (because everyone uses them) they it's hard to imagine them not doing the job well.
The other inevitable part of the problem is that each of these systems was designed and deployed at a different time, usually from different companies, with different agendas and an incentive to not 'integrate'. It's not like all of these software and systems developers are sitting in the same room discussing how they can solve the interoperability problem. Each of them is trying to sell their system and protect their market share.
But I'm here to tell you that as long as construction projects are relying on word documents, excel spreadsheets and PDFs to capture, organise and track information - they will continue to suffer from the same problems.
What problems stem from using word docs, spreadsheets and PDFs?
The obvious problem is the one we have touched on: productivity (and cost).
Labour is an extremely expensive resource.
I'm not advocating for interoperable solutions to eliminate administrators and office workers. In fact, quite the opposite. Workers in the construction and industrial sectors shouldn't be wasting their time moving information back and forth. There is plenty of other work to do which adds value to projects and companies which isn't being done at the moment because of this crazy admin.
The other more silent and subtle killer of un-interoperability in construction is project managers, management, and companies having little to no idea of what's happening on their sites in real-time - which means more delays, uninformed decision making and ultimately delivering late and over budget.
These construction project personnel can't get real-time data from site, partners and other parties because it takes time to move data when it's not interoperable.
The site diaries and daily production logs being captured on site - which are real-time reflections of how companies are tracking - are captured on documents and apps which can't be 'sucked' back into the plan to update it.
Instead, foremen take a few days to get their diaries uploaded and sent to the office, then someone in the office converts this information into a spreadsheet, then that person sends that spreadsheet to the project manager who puts the numbers into their own spreadsheet to see how they are tracking.
All of this takes days, weeks and even months. By the time this data has been collected, aggregated and analysed, the project could already be days, weeks or months behind schedule.
And while all this information was being manipulated and reconciled, management have been making decisions about what to do and what not to do - based largely on fragmented pieces of data trickling in; without the full picture.
How your company can mitigate and ultimately eliminate interoperability
It would be a bit pointless if we went through this entire interoperability mouthful and maze without providing a solution.
The solution for construction (and other industrial companies) lies in changing the source of the original documents, forms, processes and procedures.
How and where the source of information or 'data' is being captured is the important part of your entire information stack.
What does this mean in practical terms?
It means that these companies must digitise how they capture information at the site level. Foremen and engineers need to capture information in a format which the same system can understand and pass through to the office - in real-time.
The critical part of a system like this is that data is digital and standardised from start to finish. Data and information flows freely from your lists and databases, to the forms and documents being filled out on site, all the way through to your dashboards and tracking charts.
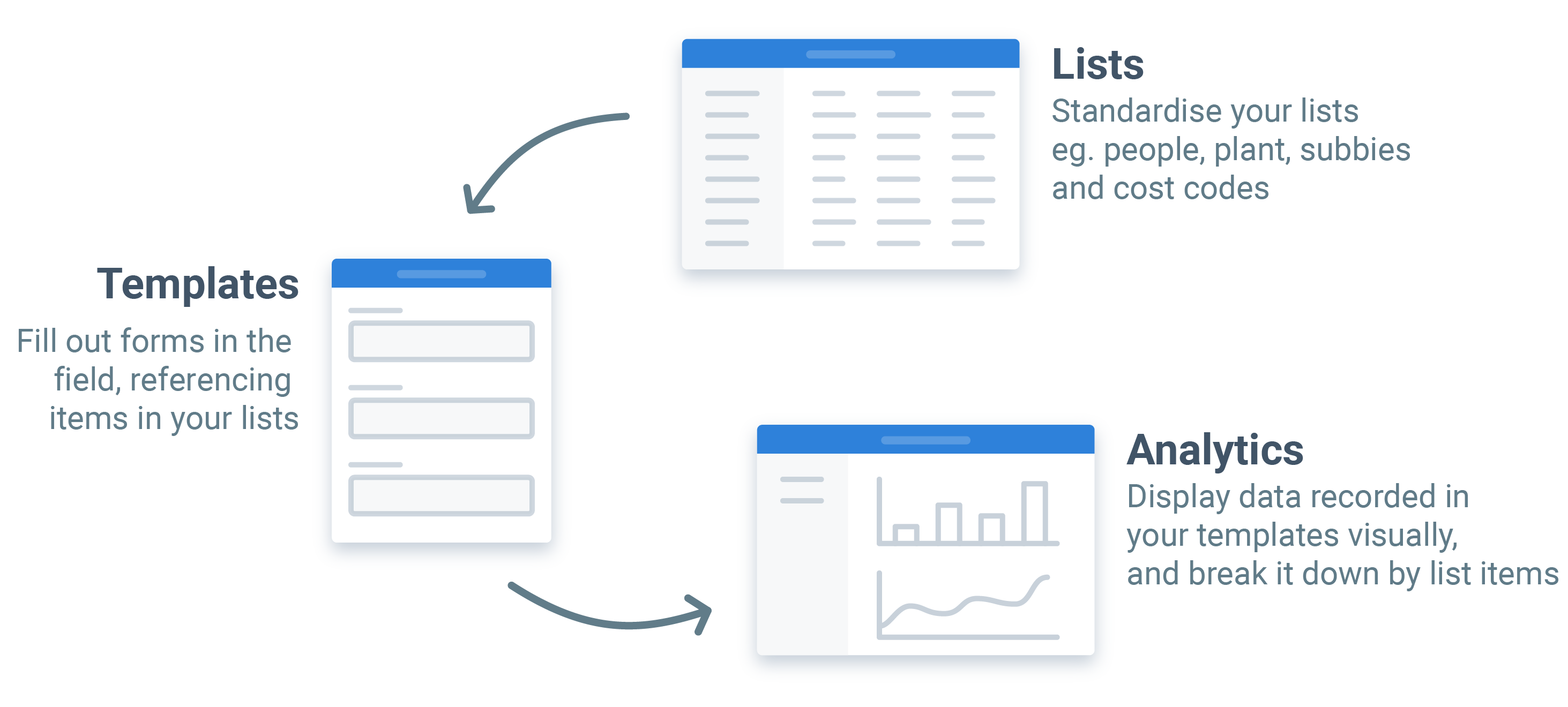
What does an interoperable future for the industries look like?
An entirely interoperable company or industry is unlikely for a long time yet. Legacy systems and processors are so tightly intertwined with how companies operate that it may take a couple of years for people to migrate to systems which enable full spectrum interoperability.
But we have seen dramatic improvements with systems and softwares in recent years, which now enable large scale interoperability for much more than a single activity or element of the business. Fully integrated management systems can now make the information being captured on site fully compatible with how people in the office want to interpret, manage and distribute that data - without ever having to bundle a bunch of sheets together, sit down and open excel for a long manual data entry sesh.
An interoperable future for the industries would usher in an age of smart and productive work. People spending their time doing their jobs efficiently, companies being able to look at and make decisions from there data - not simply shift it from one system to another.
And yes, projects being proactively managed based on real-time information which results in your company delivering on time and on budget.